Safety Equipment Installation and Maintenance Services, Kampala, Uganda
Our Expertise:
-
Comprehensive Installation:
Rely on our skilled technicians for the seamless installation of safety equipment, encompassing fire suppression systems, emergency lighting, and more. We prioritize precision, ensuring your workplace is fortified against potential hazards.
-
Proactive Maintenance:
We understand the critical importance of regular maintenance in sustaining the reliability of safety equipment. Our proactive approach guarantees that your safety systems are always in optimal condition, ready to respond effectively when needed.
-
Tailored Solutions:
Recognizing the unique safety requirements of each organization, Isazeni Solutions offers customized installation and maintenance plans. This personalized approach ensures your safety measures align with industry regulations while meeting the specific needs of your business.
-
Regulatory Compliance:
Stay ahead of safety regulations with our expertise. Our services are designed to ensure that your safety equipment not only meets but exceeds the required standards, providing peace of mind and safeguarding your workforce.
-
Innovative Technology:
Benefit from our embrace of cutting-edge technology. Isazeni Solutions stays at the forefront of safety advancements, integrating the latest innovations into our installation and maintenance services to enhance the overall effectiveness of your safety systems.
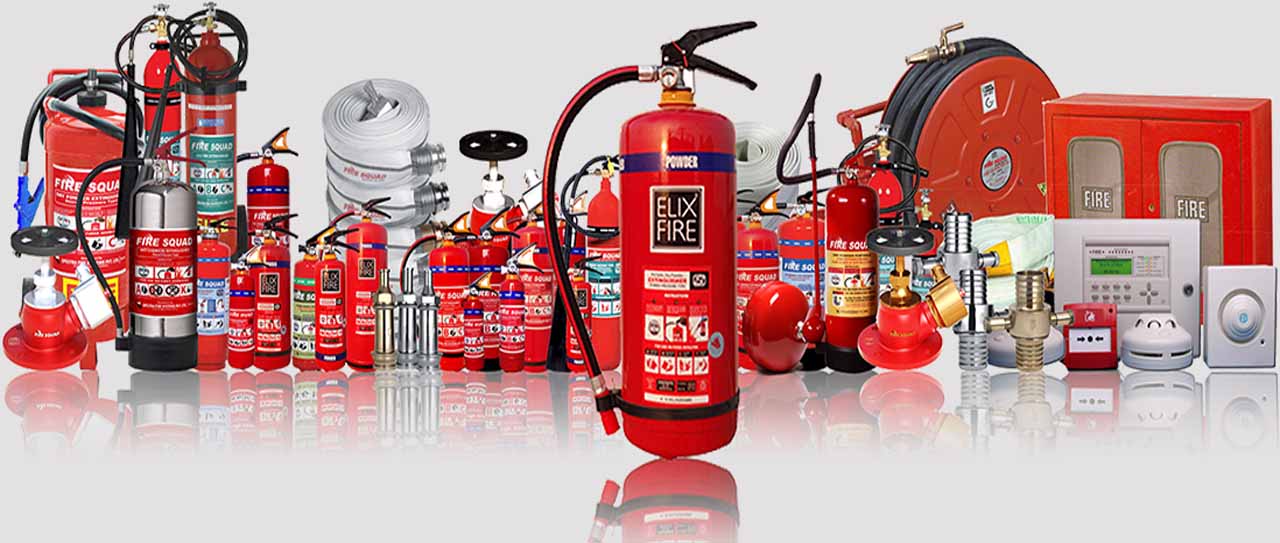
Why Choose Isazeni Solutions?
-
Experience:
Tap into the proficiency of our seasoned technicians, boasting in-depth knowledge and hands-on experience in safety equipment installation and maintenance.
-
Reliability:
Count on us for reliable and prompt services. We understand the critical nature of safety, and our team is committed to ensuring your systems are operational at all times.
-
Personalized Approach:
Isazeni Solutions believes in a client-centric approach, tailoring our services to meet the unique safety needs of your organization. Your safety is our priority, and our solutions are crafted with your specific requirements in mind.
-
Timely Response:
Enjoy peace of mind with our swift and responsive services. In emergencies or routine maintenance, we prioritize timely responses to ensure your safety systems are always prepared.
-
Continuous Improvement:
Partner with Isazeni Solutions for a commitment to continuous improvement. We actively seek feedback, invest in training, and stay updated with the latest safety standards, providing you with evolving and enhanced safety solutions.
Contact Isazeni Solutions today to fortify your workplace with our top-tier Safety Equipment Installation and Maintenance Services in Kampala, Uganda. Prioritize safety, secure your business, and stay compliant with our expert solutions. Your peace of mind is our commitment.
Secure Your Workplace Today.
What is Safety Equipment Installation Services?
Safety Equipment Installation Services involve the meticulous and professional setup of various safety systems within a workplace. The goal is to establish a robust and customized safety infrastructure that aligns with the specific needs, layout, and nature of the organization.
Components Safety Equipment Installation Services:
-
Fire Suppression Systems Installation:
– Our team specializes in the precise installation of fire suppression systems tailored to your workplace. This includes strategically placing fire extinguishers, installing sprinkler systems, and implementing advanced technologies designed to swiftly detect and control fires, ensuring the safety of your premises.
-
Emergency Lighting Installation:
– We design and install emergency lighting systems strategically throughout your facility. These lights are equipped to activate during power outages or emergencies, providing clear guidance to exits and critical areas. Our focus is on creating a well-lit evacuation path to prevent panic and ensure the safety of occupants.
-
Alarm Systems Installation:
– Our experts strategically install audible and visual alarm systems to promptly alert occupants in case of emergencies. These systems are meticulously placed to ensure maximum coverage, facilitating a quick and organized response to potential hazards, and enhancing overall safety.
-
Security Camera Installation:
– Enhance your workplace security with our professional installation of surveillance cameras. We strategically position cameras to monitor key areas, acting as a deterrent to potential threats. The footage provided by these cameras serves as a valuable tool for investigations and contributes to overall safety.
-
Access Control Systems Installation:
– Our team specializes in the installation of access control systems to restrict and monitor entry to specific areas within your organization. This additional layer of security ensures that only authorized personnel can access designated spaces, enhancing overall workplace safety.
-
Personal Protective Equipment (PPE) Distribution:
– We provide comprehensive distribution and setup of Personal Protective Equipment (PPE) for your workforce. This includes safety vests, helmets, goggles, gloves, and other necessary items tailored to your industry and workplace requirements.
-
Hazard Signage Placement:
– Our team strategically places hazard signage in areas where specific safety precautions are necessary. Clear and visible signage ensures that individuals are informed about potential risks, contributing to heightened awareness and overall safety.
-
Safety Training and Awareness Programs:
– We offer specialized safety training and awareness programs designed to educate your employees about the proper use of safety equipment and procedures. Fostering a culture of safety within your organization is our priority.
-
Ergonomic Workspace Design:
– Our experts consider ergonomic principles in designing workspaces to minimize the risk of injuries. From workstation layouts to equipment placement, our focus is on creating a comfortable and safe environment for your employees.
-
Fall Protection Systems Installation:
– Ensure the safety of employees working at elevated surfaces with our professional installation of fall protection systems. This includes guardrails, safety nets, and personal fall arrest systems, providing a comprehensive approach to fall prevention.
Request a Safety Assessment.
What are Safety Equipment Maintenance Services:
Definition: Safety Equipment Maintenance Services involve the ongoing care, inspection, and upkeep of installed safety systems. The primary objective is to ensure that these systems remain operational, compliant with regulations, and ready to respond effectively in case of emergencies.
Components of Safety Equipment Maintenance Services:
-
Regular Inspections:
Our routine inspections involve meticulous examinations of safety equipment to identify signs of wear, damage, or malfunction. Regular checks are conducted to prevent potential issues before they compromise the effectiveness of safety systems.
-
Testing Procedures:
Scheduled testing of safety systems is crucial to verify their functionality. This includes comprehensive fire alarm tests, emergency lighting checks, and other assessments to confirm that each component is operating as intended.
-
Component Checks:
Our team conducts detailed examinations of individual parts of safety equipment, such as sensors, alarms, extinguishers, and fall protection systems. This ensures that each element is in proper working condition, contributing to the overall efficacy of the safety system.
-
Documentation and Record-Keeping:
Proper documentation is maintained with detailed records of installation dates, inspection results, and maintenance activities. This record-keeping is essential for demonstrating compliance with safety regulations and providing a comprehensive history of system performance.
-
Emergency Response Planning
:
We collaborate with organizations to develop and refine emergency response plans, ensuring that safety systems align with the organization’s evolving needs and regulatory requirements. This proactive approach enhances overall preparedness.
-
Upgrades and Modernization:
Periodic upgrades and modernization of safety systems are undertaken to incorporate the latest technology and innovations. This ensures that your organization benefits from advancements in safety equipment, maintaining cutting-edge solutions.
-
Training Program Updates:
We regularly update safety training programs to keep employees informed about the latest safety procedures, equipment usage, and any changes in regulations. Ongoing training ensures that your workforce is well-prepared for any safety scenario.
-
Environmental Monitoring Systems Maintenance:
We provide maintenance for environmental monitoring systems, including air quality and gas detection systems. This ensures a safe and healthy workplace environment, with regular checks to guarantee optimal system performance.
-
Continuous Improvement Initiatives:
Our continuous improvement initiatives are based on feedback, incidents, and evolving safety standards. We actively seek opportunities to enhance the overall effectiveness of safety systems, ensuring ongoing optimization.
-
Root Cause Analysis:
In the event of safety incidents or equipment failures, we conduct thorough root cause analyses to identify underlying issues. This proactive approach allows us to implement preventive measures and avoid similar occurrences in the future.
Elevate Safety, Contact Us.
Importances of Safety Equipment Installation Services and Safety Equipment Maintenance Services for your work environment?
In any workplace, safety is non-negotiable. Achieving a secure environment involves two essential pillars: Safety Equipment Installation Services and Safety Equipment Maintenance Services. These services work hand-in-hand to establish a robust safety framework, safeguarding against potential risks and ensuring a quick response during emergencies.
10 Importance of Safety Equipment Installation Services:
Safety begins with proper installation. From fire suppression systems to emergency lighting, these installations actively reduce risks, comply with regulations, and create a proactive environment for emergencies. Compliance not only ensures legal adherence but also builds a positive reputation, showcasing a commitment to everyone’s safety.
-
Risk Mitigation:
Installation of safety equipment, such as fire suppression systems and emergency lighting, actively mitigates potential risks and minimizes the impact of emergencies like fires or power outages.
-
Compliance with Regulations:
Ensuring the installation of safety equipment is in line with local, national, and industry-specific regulations guarantees that companies comply with safety standards and avoid legal repercussions.
-
Asset Protection:
Safety installations, particularly security systems, protect valuable assets by deterring unauthorized access and monitoring areas prone to theft or vandalism.
-
Personnel Safety:
Installation of Personal Protective Equipment (PPE) stations and safety signage ensures the well-being of employees by creating awareness and providing necessary protective gear.
-
Emergency Response Enhancement:
Alarm systems and exit signage installations enhance emergency response capabilities, enabling quick and effective evacuation during crises.
-
Workplace Productivity:
A safe and secure environment fosters employee confidence and morale, positively impacting productivity and reducing absenteeism due to accidents or concerns about safety.
-
Insurance Premium Reduction:
Companies with robust safety installations often qualify for lower insurance premiums as insurers recognize the reduced risk of accidents and damage.
-
Brand Reputation:
Demonstrating a commitment to safety through proper installations enhances a company’s reputation, fostering trust among clients, customers, and partners.
-
Sustainable Operations:
Safety equipment installations contribute to sustainability by preventing accidents and minimizing environmental impact, aligning with corporate social responsibility initiatives.
-
Emergency Preparedness:
Safety equipment installations, such as fire suppression systems, ensure that companies are well-prepared to handle emergencies, reducing the potential for panic and chaos.
10 Importance of Safety Equipment Maintenance Services:
Maintenance is the ongoing assurance of reliability. Regular checks, testing, and preventive measures extend the lifespan of safety equipment, provide compliance evidence, and contribute to cost savings by identifying issues early. Maintenance services also bring continuous improvement, incorporating upgrades to keep safety systems up-to-date with the latest technology.
-
Reliability of Safety Systems:
Regular maintenance ensures that safety systems, such as fire extinguishers and alarms, are reliable and operational when needed, preventing equipment failures during emergencies.
-
Compliance Assurance:
Maintenance activities, including inspections and testing, provide documented evidence of compliance with safety regulations, reducing the risk of fines or penalties.
-
Extended Equipment Lifespan:
Routine maintenance, including component checks and replacements, extends the lifespan of safety equipment, optimizing the return on investment for companies.
-
Prevention of System Deterioration:
Maintenance prevents the deterioration of safety equipment due to environmental factors, ensuring systems function effectively and are not compromised by wear and tear.
-
Reduced Emergency Response Time:
Well-maintained safety systems respond more rapidly during emergencies, minimizing the time it takes to suppress fires, evacuate premises, or address other safety concerns.
-
Cost Savings:
Proactive maintenance helps identify and address issues before they escalate, reducing the likelihood of costly emergency repairs or the need for premature equipment replacement.
-
Employee Training and Awareness:
Maintenance activities provide opportunities for employee training and awareness, ensuring personnel are familiar with safety protocols and can respond effectively in emergencies.
-
Continuous Improvement:
Maintenance services facilitate continuous improvement by incorporating upgrades and modernization, keeping safety systems aligned with the latest technological advancements and regulations.
-
Data-Driven Decision-Making:
Maintenance activities generate valuable data on equipment performance, enabling informed decision-making regarding replacements, upgrades, and improvements to enhance overall safety.
-
Preventive Measures Implementation:
Maintenance services allow for the implementation of preventive measures based on historical data, reducing the likelihood of recurring issues and enhancing the overall effectiveness of safety systems.
Explore Safety Solutions Now
How much are Safety Equipment Installation Services and Safety Equipment Maintenance Services?
Certainly! Below are two price tables, one for Safety Equipment Installation Services and the other for Safety Equipment Maintenance Services. I’ve also included a section in the maintenance table indicating how often maintenance is typically required.
Safety Equipment Installation Services Price Table:
Service |
Description |
Price RANGE |
Fire Suppression Systems Installation | Installation of automatic sprinklers and fire extinguishers | $500 – $1,000 |
Emergency Lighting Installation | Installation of exit signs and emergency light fixtures | $1,000 – $2,500 |
Alarm Systems Installation | Installation of smoke detectors, heat detectors, and alarms | $800 – $1,500 |
Personal Protective Equipment (PPE) Installation | Installation of safety signage, PPE stations, and dispensers | $1,200 – $2,000 |
Security Systems Installation | Installation of access control systems and surveillance cameras | $600 – $1,200 |
Safety Equipment Maintenance Services Price Table:
Service |
Description |
Price RANGE |
Regular Inspections | Scheduled inspections to check the condition of safety equipment | $500 – $1,000 |
Testing Procedures | Routine testing of safety systems, including fire suppression and alarms | $1,000 – $2,500 |
Component Checks | Examination of individual components for wear and tear | $800 – $1,500 |
Documentation and Record-Keeping | Maintenance of detailed records for compliance | $1,200 – $2,000 |
Upgrades and Modernization | Assessment and implementation of upgrades for enhanced efficiency | $600 – $1,200 |
Safety Equipment Maintenance Frequency:
The frequency of maintenance for safety equipment can vary based on factors such as equipment type, environmental conditions, and regulatory requirements. Below is a general guideline for maintenance intervals:
- – Regular Inspections: Quarterly
- – Testing Procedures: Semi-annual
- – Component Checks: Annually
- – Documentation and Record-Keeping: Continuous
- – Upgrades and Modernization: As needed or every 3-5 years
Note or Disclaimer:
The prices outlined in the tables below are indicative and are intended to provide a general overview of potential costs associated with Safety Equipment Installation and Maintenance Services. It’s important to note that these figures are organizational-based estimates and may vary based on several factors, including the size and complexity of the installation, the specific requirements of your organization, and the prevailing market conditions.
Organizational-Based Estimates:
The provided prices are meant to serve as a starting point for organizations seeking an understanding of potential budget considerations. However, we strongly recommend contacting our team for a detailed consultation to assess your unique needs and receive a customized quote tailored to your specific requirements.
Variables Impacting Pricing:
Factors such as the type and quantity of safety equipment, the complexity of installation, and the frequency of maintenance can significantly influence the final cost. Our team will work closely with you to understand these variables and provide a more accurate and personalized cost estimate based on a comprehensive assessment.
Request a Consultation:
For precise pricing information and to discuss the specific needs of your organization, we invite you to reach out to our team for a consultation. This will enable us to better understand your requirements, recommend tailored solutions, and provide a detailed and accurate quotation.
Your safety is our priority, and we are committed to delivering solutions that align with your organizational goals and budget considerations. Contact us today to embark on a comprehensive safety journey that ensures the well-being of your workforce and the protection of your assets.
Ensure Compliance, Schedule Maintenance.
Frequently Asked Questions (FAQs)
1. What is Safety Equipment Installation Services?
2. What are Safety Equipment Maintenance Services?
3. Why is Safety Equipment Installation important for businesses?
5. What types of safety equipment does Isazeni Solutions install?
6. How often should safety equipment be inspected and maintained?
7. Does Isazeni Solutions provide safety training for employees?
8. How does Isazeni Solutions ensure compliance with safety regulations?
9. What are the benefits of installing security cameras and access control systems?
10. How does Isazeni Solutions integrate new technologies into safety solutions?
11. Can Isazeni Solutions customize safety solutions for specific industries?
12. What is included in Isazeni’s emergency response planning services?
13. How much do Safety Equipment Installation and Maintenance Services cost?
14. Does Isazeni Solutions offer one-time installations or ongoing maintenance contracts?
15. How can I request a safety assessment from Isazeni Solutions?
16. How quickly can Isazeni Solutions respond to emergency safety concerns?
17. What makes Isazeni Solutions a trusted provider of safety services in Kampala?
18. What industries does Isazeni Solutions serve?
19. How does Isazeni Solutions ensure quality and reliability in its installations?
20. Can Isazeni Solutions upgrade existing safety systems?
21. Does Isazeni Solutions offer warranties on safety equipment installations?
22. What should businesses do if a safety system malfunctions?
23. How does Isazeni Solutions help businesses save costs on safety equipment?
24. Can Isazeni Solutions integrate multiple safety systems into a single platform?
25. Does Isazeni Solutions provide customized safety signage and labels?
26. What are some common workplace hazards that Isazeni Solutions can help mitigate?
Fire hazards – through fire detection, suppression, and evacuation planning.
Slips, trips, and falls – with anti-slip flooring, proper lighting, and fall protection systems.
Unauthorized access – via security cameras, biometric access control, and perimeter security.
Electrical hazards – with surge protection, safety signage, and regular inspections.
Chemical exposure – through proper ventilation, hazardous material storage, and PPE.
Our team conducts risk assessments to identify and address potential dangers, ensuring a safer work environment.
27. How does Isazeni Solutions handle fire safety compliance for businesses?
28. What emergency response solutions does Isazeni Solutions provide?
Fire suppression and alarm systems for early detection and automatic fire control.
Emergency lighting and exit signs to guide employees during evacuations.
Panic alarm systems for quick response to security threats.
First aid stations and medical emergency plans to address workplace injuries.
Evacuation drills and staff training to ensure readiness for different emergencies.
We tailor these solutions to suit different workplace environments and risk levels.
29. Can Isazeni Solutions provide security solutions for residential properties?
CCTV camera installations for real-time home surveillance.
Burglar alarms and motion sensors to detect intrusions.
Smart access control systems to manage entry points securely.
Fire and smoke detectors to enhance household safety.
We offer customized packages to meet the unique security needs of homeowners, apartment complexes, and gated communities.
30. How can I book a consultation with Isazeni Solutions?
Phone: Call our customer service team for immediate assistance.
Email: Send us an inquiry, and we’ll respond with details.
Website: Fill out our online contact form to schedule an assessment.
In-Person Visit: Stop by our office in Kampala, Uganda, for a face-to-face consultation.
Our team will evaluate your safety needs and provide expert recommendations to ensure your workplace or residence is secure.
31. How often should businesses schedule safety equipment maintenance with Isazeni Solutions?
32. Can Isazeni Solutions help businesses obtain safety compliance certification?
33. What types of fire suppression systems does Isazeni Solutions install?
Sprinkler Systems – for automatic fire control in commercial buildings.
CO2 Fire Suppression – ideal for server rooms and electrical hazards.
Foam-Based Systems – for areas with flammable liquids, such as fuel storage.
Dry Chemical Systems – for industrial kitchens and high-risk workplaces.
We assess your facility and recommend the most suitable fire suppression system based on your specific fire risks.
34. How does Isazeni Solutions ensure workplace safety training is effective?
35. Does Isazeni Solutions offer energy-efficient safety solutions?
LED emergency lighting for lower energy consumption and longer lifespan.
Solar-powered security systems to enhance sustainability.
Smart fire detection and suppression systems that use minimal resources.
Motion-sensor surveillance cameras that optimize power usage.
Our energy-efficient solutions provide long-term cost savings while minimizing the environmental impact of safety operations.
36. What steps does Isazeni Solutions take before installing a safety system?
Risk Assessment – We identify workplace hazards and vulnerabilities.
Consultation & Planning – We work with clients to develop a customized safety solution.
Equipment Selection – We recommend high-quality, industry-approved safety equipment.
Installation & Configuration – Our experts set up the system for maximum efficiency.
Testing & Verification – We conduct thorough testing to confirm operational reliability.
Training & Handover – We educate staff on system use and emergency protocols.
This process ensures a smooth and effective implementation of safety solutions tailored to each client’s needs.
37. Can Isazeni Solutions help with security surveillance system monitoring?
38. Does Isazeni Solutions offer biometric access control systems?
Fingerprint scanners for office and industrial facilities.
Facial recognition systems for high-security areas.
Iris scanners for sensitive government and healthcare institutions.
Multi-factor authentication combining biometrics with PIN codes or RFID cards.
These systems provide an efficient, secure, and tamper-proof way to control access to sensitive areas.
39. How does Isazeni Solutions enhance workplace emergency preparedness?
Evacuation route planning with clearly marked emergency exits.
Fire and security drills to ensure employees are trained for emergencies.
Emergency communication systems for rapid response coordination.
First aid stations and medical kits to address workplace injuries.
Automated alert systems for fire, security breaches, and natural disasters.
By implementing these measures, businesses can ensure a quick, efficient response to emergencies, reducing potential risks and damage.
40. How does Isazeni Solutions support long-term safety system maintenance?
Regular inspections and system testing to detect and fix potential failures.
Preventative maintenance to extend the lifespan of safety equipment.
Software updates for smart security and fire detection systems.
Emergency repairs and 24/7 technical support to address unexpected malfunctions.
Our maintenance services help businesses avoid costly system failures, ensure compliance, and maintain workplace safety at all times.
42. How does Isazeni Solutions handle large-scale safety projects?
Initial Consultation – Understanding client needs and defining project scope.
Detailed Safety Audit – Identifying all risk factors and compliance requirements.
Customized System Design – Developing tailored safety and security solutions.
Project Implementation – Professional installation by certified technicians.
Quality Assurance & Compliance Checks – Ensuring the system meets regulatory standards.
Ongoing Maintenance & Support – Providing continuous monitoring and updates.
This structured approach allows us to successfully handle complex safety installations across multiple sites and industries.
43. What industries benefit from Safety Equipment Installation and Maintenance Services?
44. How do Safety Equipment Services contribute to workplace safety culture?
45. What is the process for scheduling Safety Equipment Installation or Maintenance?
46. How does Isazeni Solutions ensure compliance with Ugandan and international safety regulations?
47. What emergency support services does Isazeni Solutions offer?
48. Can businesses receive customized safety training alongside installation and maintenance services?
49. How does technology enhance safety equipment performance and reliability?
50. Why should organizations invest in long-term safety maintenance plans?
51. How often should safety equipment be inspected and maintained?
52. What factors should businesses consider when choosing a safety equipment provider?
53. How does Isazeni Solutions support small businesses with safety compliance?
54. Can Isazeni Solutions assist businesses with fire safety audits and risk assessments?
55. How does Isazeni Solutions handle large-scale safety equipment installations?
56. What role does preventive maintenance play in safety equipment reliability?
57. What are the key benefits of partnering with Isazeni Solutions for safety services?
58. How does Isazeni Solutions ensure compliance with safety regulations?
59. Does Isazeni Solutions offer safety training for employees?
60. What industries does Isazeni Solutions serve?
Corporate offices – Access control, fire alarms, and surveillance systems
Manufacturing & industrial plants – Fire suppression, PPE, and hazard detection
Hospitality & retail – CCTV, emergency lighting, and fire safety solutions
Healthcare facilities – Smoke detectors, evacuation plans, and infection control
Educational institutions – Fire drills, security systems, and first aid training
Regardless of the industry, we customize safety solutions to fit the specific risks and operational needs of our clients.
61. How does Isazeni Solutions handle emergency maintenance requests?
62. What technology does Isazeni Solutions use in safety equipment?
63. Can Isazeni Solutions customize safety solutions for specific business needs?
64. Does Isazeni Solutions provide warranties on installed safety equipment?
65. How does Isazeni Solutions support businesses in disaster preparedness?
66. What are the signs that safety equipment needs servicing or replacement?
Frequent false alarms in fire detection and security systems
Visible wear and tear on fire extinguishers, alarms, or PPE
Failure to activate during routine testing
Unresponsive emergency lighting or access control systems
Outdated equipment that does not meet current safety regulations
At Isazeni Solutions, we offer regular safety audits and system diagnostics to detect and fix potential issues before they compromise workplace safety.
66. What are the signs that safety equipment needs servicing or replacement?
Frequent false alarms in fire detection and security systems
Visible wear and tear on fire extinguishers, alarms, or PPE
Failure to activate during routine testing
Unresponsive emergency lighting or access control systems
Outdated equipment that does not meet current safety regulations
At Isazeni Solutions, we offer regular safety audits and system diagnostics to detect and fix potential issues before they compromise workplace safety.
67. What maintenance contracts does Isazeni Solutions offer?
68. How can businesses schedule a consultation with Isazeni Solutions?
69. Does Isazeni Solutions offer any post-installation support services?
69. Does Isazeni Solutions offer any post-installation support services?
70. What makes Isazeni Solutions different from other safety equipment providers?
71. How does Isazeni Solutions ensure the safety of its own workers during installations?
72. Can Isazeni Solutions install and maintain security systems in residential properties?
73. Does Isazeni Solutions offer safety equipment for hazardous work environments?
74. How can I get a quote for Isazeni Solutions' services?
75. Can Isazeni Solutions handle the installation of complex fire suppression systems?
76. What steps does Isazeni Solutions take to ensure the reliability of its safety equipment?
77. Does Isazeni Solutions provide energy-efficient safety equipment?
78. How long has Isazeni Solutions been in the safety equipment industry?
79. Can Isazeni Solutions provide safety equipment for schools and educational institutions?
80. Does Isazeni Solutions offer safety training services?
81. How does Isazeni Solutions keep up with changing safety regulations?
82. Can Isazeni Solutions help with risk assessments for my business?
83. How does Isazeni Solutions ensure the quality of its products?
84. Can Isazeni Solutions handle emergency repairs for safety equipment?
85. Does Isazeni Solutions offer security systems for warehouses and industrial facilities?
86. Can Isazeni Solutions install safety equipment in government buildings?
87. How long does the installation process take for safety equipment?
88. What kind of warranties does Isazeni Solutions offer on safety equipment?
89. Can Isazeni Solutions help businesses with insurance-related safety requirements?
90. How can Isazeni Solutions assist with disaster preparedness planning?
91. Can Isazeni Solutions provide integrated safety and security systems?
92. What types of industries does Isazeni Solutions serve?
93. How does Isazeni Solutions ensure the privacy of sensitive data?
94. Can Isazeni Solutions provide 24/7 monitoring services for my security systems?
95. How can I request a consultation for my business from Isazeni Solutions?
96. Does Isazeni Solutions offer fire safety solutions for residential properties?
97. What makes Isazeni Solutions different from other safety service providers?
98. How do I know if my existing safety systems need upgrading?
99. Can Isazeni Solutions help my business with health and safety compliance?
100. Can Isazeni Solutions handle large-scale safety system installations for multi-site businesses?
TECHNOLOGY PARTNERS WE USE IN WESITES & RELATED SERVICES
For years we have acquired strategic partnerships enabling us to serve you better
Ready to start on your project? let’s jump into it.